What is Vacuum Casting Service?
Vacuum casting services is a manufacturing process for creating small batches of high-quality plastic parts that simulate the properties of injection-molded parts. This process involves creating a silicone rubber mold of the master part, which is then used to make multiple copies of the part through the use of liquid polyurethane resin under vacuum conditions. OrideTech’s vacuum casting service is set for you to make plastic parts in lower cost and faster lead time, especially when your development parts are in prototyping and low-volume production. If the product quantity is around 100pcs or less, OrideTech vacuum casting services is your best choice to make samples. For more details and videos, you can review on our Facebook page or YouTube channel.
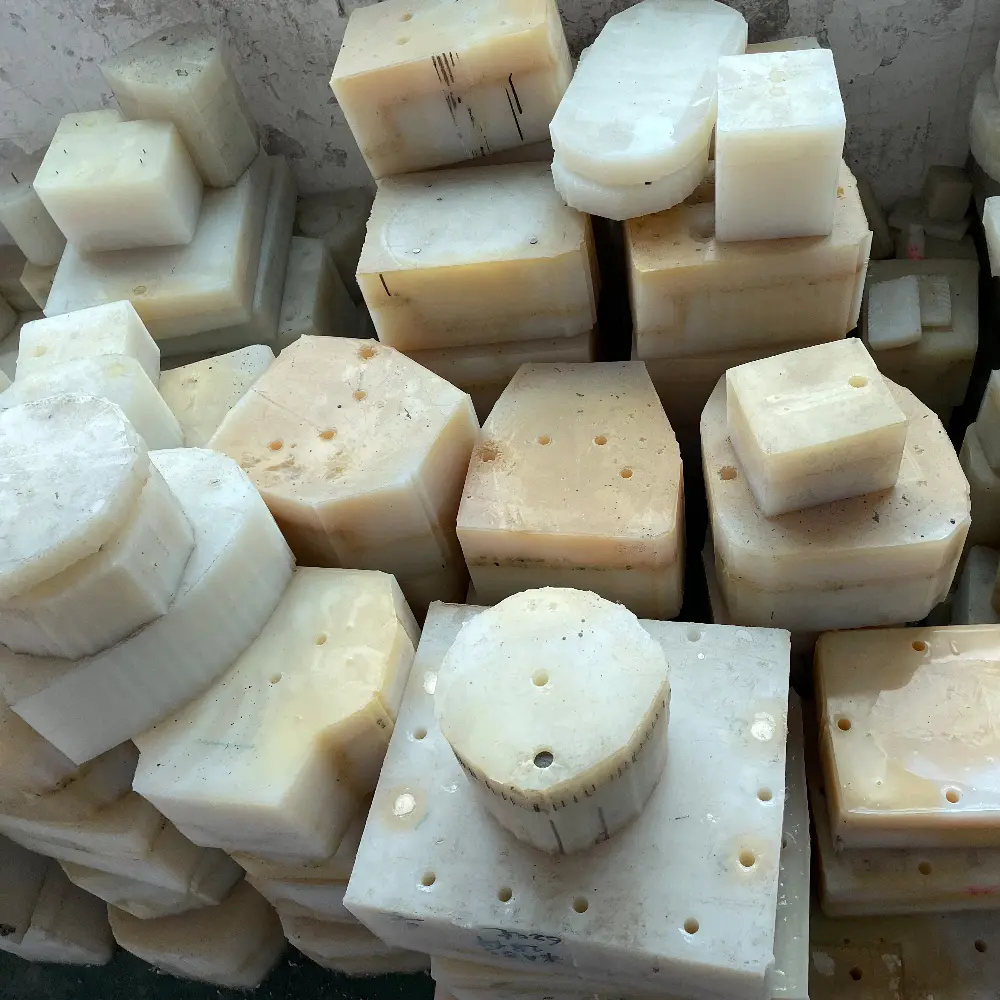
Advantages of Vacuum Casting Services
OrideTech sets vacuum casting services and have been providing vacuum casting samples to customer for many years. Compared with other plastic parts process like CNC machining, 3D printing and injection molding, vacuum casting has many advantages
- It can produce high-quality parts with excellent surface finishes and fine details.
- The process is also relatively fast and cost-effective compared to injection molding.
- It allows for the use of a variety of materials and colors, making it highly versatile.
- It can support your design flexibility and manufacturing flexibility during prototyping.
- It is perfect to rapid prototype samples and low-volume production, and being bridge to production.
Material Used in Vacuum Casting Services
The vacuum casting services support variety of materials. The main materials are polyurethane, epoxy, silicone, and other thermoplastic and thermosetting polymers. Different materials offer different properties, such as flexibility, hardness, and resistance to chemicals or temperature. By choosing the right material for the application, it is possible to create vacuum casting parts with a wide range of properties and performance characteristics. Oridetech stocked many common use vacuum casting materials for your urgent projects in both prototyping and low-volume production. If you choose the available material in our stock, your will get the parts in lower cost and less time.
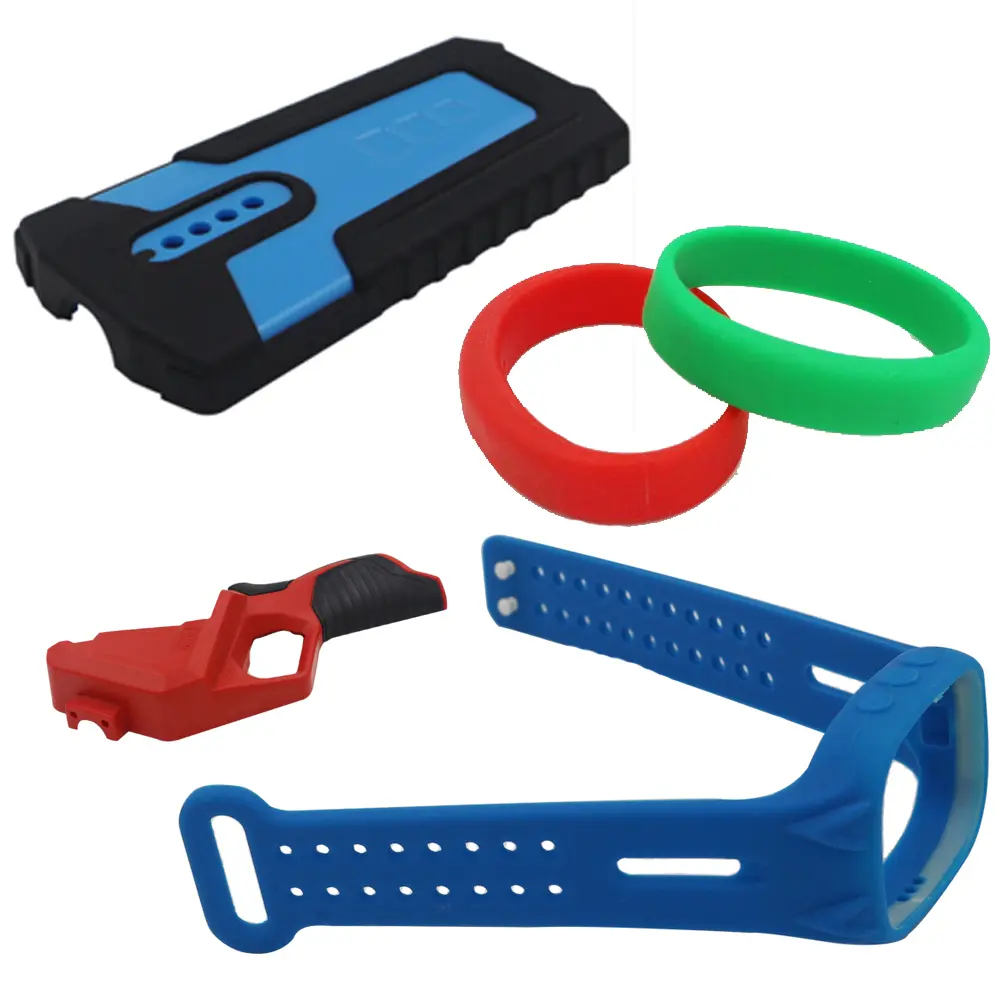
Vacuum Casting Tolerances and Limitations
Generally, OrideTech vacuum casting services can make parts in tolerance of +/-0.10mm. However, the precision can vary depending on several factors, including the geometry of the part, the material, and the level of post-processing. The vacuum casting mold life depends on several factors, the material, the complexity of the part, and the amount of wear and tear experienced during process. OrideTech silicone rubber molds using in vacuum casting can last for anywhere from 20 to 30 casts before showing signs of damage.
OrideTech Vacuum Casting Steps
Step 1 Master Patterns:
OrideTech uses CNC machining or 3D printing like SLA/SLS technology to make high accuracy patterns for vacuum casting
Step 2 Making the molds:
OrideTech uses liquid silicone to make the molds. This silicone material is poured around the master inside of a casting box and then removed by cut open the molds after curing in oven for 16 hours. The empty cavity in the casting box is for casting.
Step 3 Casting Copies:
The customer chose resins which can be poured into the empty cavity to create a highly accurate copy of the original. And the process also can do over-molding with two or more materials. This silicone molds have a life span of about 20 times.
Step 4 Apply finishing:
OrideTech provides many finishing processes like painting, silk printing, laser marking for your parts.
Why Choose OrideTech for Vacuum Casting Services?
OrideTech has provided vacuum casting parts for many years. And most parts from OrideTech gets high praise from our customers. The vacuum casting parts from OrideTech always work well in customer’s final devices. And this saved lots of money for our customers.
- Great cost saving from using vacuum casting, compared with kicking off injection molds.
- More cost-effective for small to medium-sized production runs in prototyping and low-volume production.
- Save much cost for your design changes in prototype and engineering verification test period.
- Various post-processing techniques can be used for vacuum casting parts, including painting, sandblasting, polishing, and assembly
- It supports finishing like painting specific colors, textures, and other specifications, making them suitable for a wide range of applications.